As the world seeks innovative ways to manage organic waste and improve environmental sustainability, carbon-rich materials like biochar have gained increasing attention. Biochar is a highly porous, carbon-based substance produced through pyrolysis, a process that thermally decomposes biomass in a low-oxygen environment. Its applications span across multiple industries, from agriculture to energy, offering both economic and ecological benefits.
Transforming Waste into Valuable Resources
Biomass waste, including agricultural residues, forestry waste, and organic byproducts, often ends up in landfills or is burned inefficiently, contributing to environmental pollution. However, with advanced biochar machine solutions, these materials can be converted into valuable resources. Biochar enhances soil fertility, improves water retention, and reduces greenhouse gas emissions when used in agriculture. It also serves as an essential component in carbon sequestration efforts, helping combat climate change.
The Core of the Process
The efficiency of biochar production lies in the biochar reactor, a key component of the process. This reactor is designed to operate at high temperatures, ensuring complete carbonization of biomass while minimizing emissions. Through precise temperature control and optimized reaction conditions, the reactor maximizes biochar yield while producing byproducts such as wood vinegar and tar, which can be further utilized in industrial applications.
Enhancing Value Through Briquetting
Beyond raw biochar, there is a growing demand for compressed biochar products that are easier to store, transport, and use. The charcoal briquetting machine transforms loose biochar into uniform, high-density briquettes. These briquettes offer longer burn times and higher energy efficiency, making them an ideal alternative to traditional fuels in both household and industrial settings. The use of briquetted biochar in heating, cooking, and power generation significantly reduces reliance on fossil fuels while promoting renewable energy solutions.
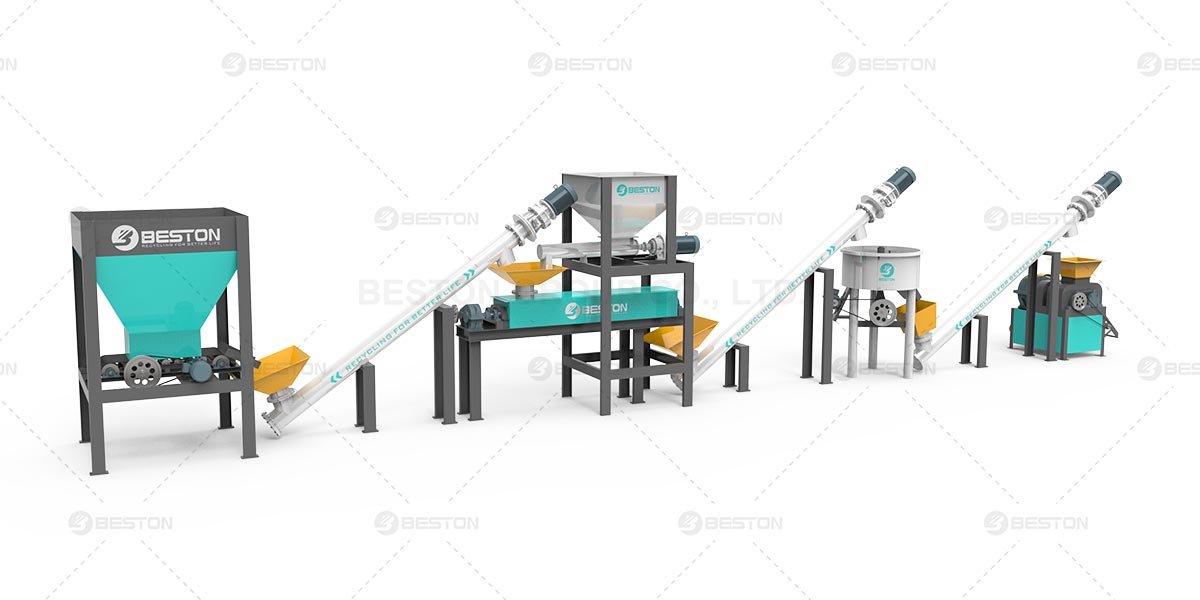
Charcoal Briquette Machine
Driving Sustainability and Circular Economy
Incorporating biochar into various industries not only creates economic opportunities but also reinforces the principles of a circular economy. Waste materials that would otherwise be discarded are given new life, reducing environmental impact and enhancing resource efficiency. Companies that adopt biochar technology contribute to sustainable land management, carbon neutrality, and improved waste valorization strategies.
Why Choose Beston?
With years of expertise in pyrolysis and biomass processing, Beston Group offers cutting-edge solutions for biochar production and utilization. Their technology ensures high efficiency, environmental compliance, and economic viability, helping businesses and individuals transition to more sustainable practices. Whether for agricultural enhancement, energy production, or waste management, Beston’s solutions provide a reliable pathway toward a greener future.
The shift toward sustainable resource management requires innovative approaches like biochar utilization. By leveraging advanced biochar production techniques, optimizing reactor efficiency, and enhancing the usability of biochar through briquetting, industries and communities can take meaningful steps toward reducing waste, improving soil health, and lowering carbon footprints. As a leader in the field, Beston Group continues to drive change, offering scalable and sustainable solutions that benefit both businesses and the environment.