Modern Waste Tire to Oil Plant
A waste tire to oil plant enables scrap rubber tires to be converted into fuel oil in an eco-friendly, effective manner. Such plants have revolutionized the rubber recycling industry in many countries. The reality is that there are millions of scrap tires that require recycling each year, so pyrolysis plant owners are able to obtain the raw materials needed to power their plants very cheaply. What’s more, many governments have introduced business grants and tax subsidies for those involved in the tire recycling industry to promote environmental responsibility.
Beston’s pyrolysis tire to oil machines are a popular choice with investors from around the world. In 2018, the company supplied a waste tyre to oil plant in South Africa, but there also have customers in the Philippines, Argentina, the UK, Norway, Australia and many other countries. The company is known for its high-grade machinery and top-rated service. Engineers from the company are available to help with plant installation, commissioning, maintenance and repairs.
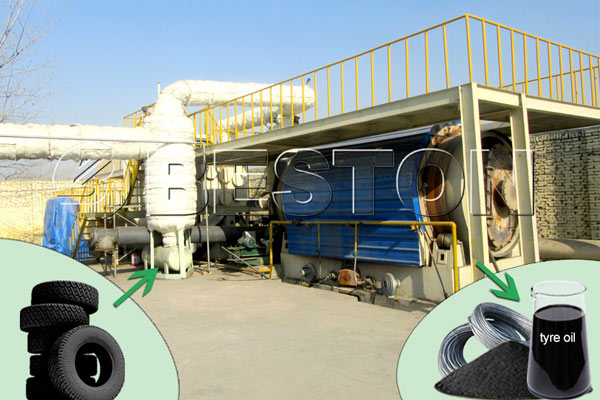
Tyre To Oil Machine
Beston currently has a wide range of tire to oil plants for sale with daily capacities ranging from six tons of waste rubber to 24 tons of waste rubber. Furthermore, all of the pyrolysis plants can also process various other forms of waste including plastics, oil sludge, medical waste, etc. The multipurpose nature of the plants means they are a great investment option for anyone looking to set up a profitable waste processing business. Click to learn the tire pyrolysis plant cost now.
When comparing pyrolysis plant models for sale, some of the parameters to take account of include reactor pattern, working method, daily capacity, total power, operating pressure, cooling method, floor area, reactor size, reactor heating fuel, service life, etc. For reference, the average service lifespan of a waste tire to oil machine reactor is between five and eight years.
When it comes to working methods, you can find batch, semi-continuous and fully continuous pyrolysis plants in the marketplace. Batch tire to oil machines typically have limited daily rubber waste processing capacities, but they are ideal for small to mid-sized tire recycling facilities that don’t have 24/7 operations. Fully continuous pyrolysis reactor, meanwhile, are the best option for rubber recycling facilities that seek to process in excess of 20 tons of scrap tires each day.
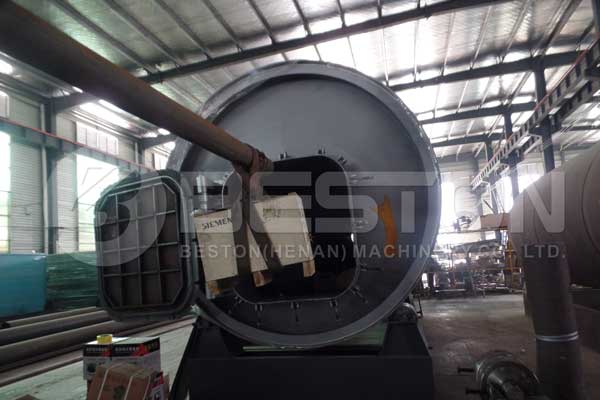
Pyrolysis Plant Cost
It’s important to note that in addition to fuel oil, waste tire to oil plants also produce three other profitable end products: carbon black, combustible gas and steel wire. A typically road tire is composed of 50% tire oil, 30% carbon black, 12% steel and 8% combustible gas. This means that 1 ton of scrape tires can be converted into around 500kg of fuel oil using a modern rubber pyrolysis reactor.
Fuel oil extracted from waste tires via pyrolysis can be sold directly to heavy industry in its raw state as heavy fuel or it can be processed further into diesel or gasoline using a distillation machine. Many tire recycling facilities opt to invest in an oil distillation machine in addition to a waste rubber pyrolysis plant, as they can make more money selling gasoline or diesel oil as opposed to tire oil.